Conditions in the workplace can change at any time. Therefore, the supervisor's / supervisor's job is to take action to adapt to these changes, and if an abnormality occurs, immediately take steps to overcome it. A supervisor must always be at the workplace and supervise the state of the production facilities including machines, workplace atmosphere and production methods.
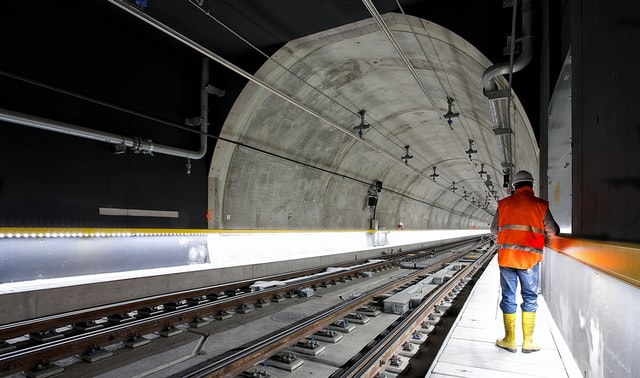
The supervisor's job is very important. Therefore it can be said that "supervisors function as the key to occupational safety and health. To control occupational safety and health in the workplace, there are 10 keys that are the obligations of supervisors in carrying out daily tasks, namely:
1. Determination of Work Procedures (Standard Operations)
In order to produce high quality quantities in larger quantities at low costs in a safe and healthy manner, the operating methods need to be standardized first. This is intended to gain understanding and cooperation from all employees in the workplace, so that it can be adhered to and implemented as well as possible.
To obtain certainty or guarantee of occupational safety and health, it is necessary to first estimate the possible hazards that will arise before starting operations, and to determine the work implementation procedure including occupational safety and health measures.
Regarding non-routine work such as repairs and inspections, it is also necessary to determine the implementation of activities. Determination of work procedures is very basic and aims to eliminate dangerous actions in the workplace.
2. Improvement of Work Methods
Supervisors should always pay attention to whether the work method / method of operation is dangerous or disruptive and try to improve the method being used in order to obtain better results. The place of production allows for movement (changes in both people and equipment. In these changes can cause problems that were not previously thought.
Although there are no problems, it is necessary to review and improve the situation to achieve the target that has been set, therefore supervisors need to master methods to improve working methods so that they can guide their subordinates in case of undesirable problems To improve conditions at work based on previous experience by following the following procedures:
• look for things that need to be fixed (realizing the problem and asking yourself questions)
• Analyzing the current method: based on facts (understanding the situation)
• Finding the problem: according to the standard (knowing the things that become the problem
• Considering how to solve it: hearing the opinion of the people concerned ( researching the way men solution)
• Implementing new methods: considering implementation results (analyzing results)
3. Correct Placement of Workers
An inspector must do the following in the placement of workers:
• Know the job needs
• Know the characteristics of workers and divide tasks according to these characteristics.
• Respond to the wishes of workers as much as possible.
• If necessary, propose a transfer / change of placement of workers to superiors.
4. Coaching and Supervision in Carrying Out Duties
Supervision means encouraging the spirit of subordinates to carry out tasks in a broad sense and directly leading and fostering subordinates in carrying out their duties in the field and directly managing materials, facilities, machines and equipment in the workplace. Several duties and responsibilities of supervisors in relation to the development and supervision of the field of Occupational Health and Safety:
• Improving “the standard of safe and healthy work implementation and instructing subordinates to comply with them.
• Improve the “voluntary checklist” and instruct subordinates to check
• Know who needs an inspection of the work atmosphere and the results of the inspection
• Improve the “extermination and cleaning standards” and instruct subordinates to comply with these standards
• Carry out the placement of workers after considering the qualifications and abilities of each worker -Each of them
• Conduct coaching / training regarding occupational safety and health "
• Carry out activities to raise awareness of subordinates regarding Occupational Safety and Health
• Make provisions to deal with emergencies or when abnormalities are found and instruct subordinates to understand these provisions
• Maintain the health of their subordinates Post instructions and signs in the workplace, which are required by regulations.
5. Increasing Occupational Safety and Health
To improve safety and work, it is necessary to take the following steps:
• Increasing safety of machine facilities
• Increasing safety of electrical facilities
• Increasing fire prevention due to explosion
• Increasing the level of safety of transportation facilities
• Increasing safety due to falls and falling hazards
6. Maintenance of work environment requirements
The main things in the implementation of tidiness and cleanliness are as follows:
• Adjusting the direction of flow of work and laying out the means of eliminating unnecessary transportation work
• Storage and storage methods for goods
• Determined corridors, doors entry / exit as well as emergency exits and always maintain the state of these places.
• Place a container to collect items that are not needed in the workplace. Items that are put in the container are collected periodically.
• For each workplace determine the area of responsibility for each area.
• An inspection is carried out to check tidiness and cleanliness is carried out.
7. Occupational Safety and Health Inspection
a. Making an inspection plan
If a supervisor makes an inspection plan, it is necessary to pay attention to the following matters:
• When (intensity of examination): determined by the time and duration
• Who (the investigator): determined who checks
• What (what is examined): facilities production, machinery, equipment, workplaces, work safety equipment, worker movements / actions
• How (method of inspection): whether visually, using equipment
b. Matters to consider at the time of inspection
When carrying out occupational safety and health checks, it is necessary to pay attention to the following:
• make workers in the workplace understand the importance of inspection and are asked to cooperate
• Avoiding attitudes or ways that look for mistakes
• The examiner provides a good example of in terms of dress and attitude
• If there has been a previous accident, it is necessary to check whether the cause of the accident is no longer there
• check whether the condition is unsafe
• If unsafe conditions are found or unsafe actions, it is necessary to check the underlying cause and take preventive measures
• It is not allowed to prioritize ease of work over safety.
• Thoroughly check the condition of machines and facilities that are usually considered trivial.
• give a warning when things are found that are wrong and give praise when the worker takes action with regard to safety
c. Making a check list
In order to simplify the examination and prevent the things that need to be checked, a check list should be made
8. Settlement at the time the abnormality is found and the time when the accident occurs.
If a situation deviates from the standard, such a situation is referred to as a mismatch or a problem is found, this situation if left untreated will result in an accident. Examples of abnormalities are:
a. Unsafe conditions:
• safety facilities and equipment from damaged or decreased capacity
• protective covers, bars and damaged installations, removed or left after removal
• meter instructions sway past normal limits
• abnormalities with sound, vibration, temperature and engine speed are found which is being operated. etc.
b. Acting unsafe:
• working without using the required personal protective equipment
• in group work indisciplined work
• keep using damaged production facilities, etc.
9. Increasing occupational safety and health awareness
Making workers understand and obey the provisions for maintaining occupational safety and health is very important in order to save lives and health. In order for workers to become accustomed to complying with these provisions, it is necessary to raise their awareness in various ways. several methods to raise awareness:
• tool box meeting methods
• utilize the proposed occupational safety and health system
• utilize the occupational safety and health picket system
• utilize morning apples
• determine occupational safety and health days
• raise awareness through occupational safety and health competitions
• utilize the system respect for occupational safety and health • make use of posters and slogans
10. Creativity to prevent occupational accidents
To develop the creativity of workers to overcome occupational safety and health problems, besides directly obtaining good results but also increasing workers' awareness. Creativity is a new method developed based on the experience and knowledge possessed by workers. Ways to increase the creativity of workers to prevent workplace accidents by:
a. Creating a good working atmosphere to increase creativity:
• problems obtained through the program so far (eg voluntary examinations, wheel checks and reports of near accident cases) are recorded as data.
• individual or group themes to discuss and make suggestions for improvement
• praise good ideas or suggestions
b. Understanding the situation together
Supervisors can get results both through the efforts of their subordinates to do the job and to improve safety but that does not mean that only subordinates are trying to make efforts together.
c. Fostering creativity
There are several types of creative abilities that are expected to be improved:
• the ability to recognize problems and look for problem factors at work (the ability to find problems)
• the ability to use basic knowledge and apply it (the ability to apply)
• the soft way of thinking, ready to replace the old way with new (thinking skills)
• based on new clues, creating new ideas (imaginary skills)
• ability to propose ideas and formulate ideas (ability to organize)
• ability to structure new ideas so that they can be used in a real way (ability to perfect
إرسال تعليق